Understanding Ultrasonic Channel Inspection: An Overview
IOnic is a technology designed for channel inspection of casted and machined parts, such as cylinder heads and engine blocks. This amazing technology is based on ultrasonic measurement. With several advantages, IOnic is the state of the art technology, bringing high quality for lower cost to your manufacturing processes.
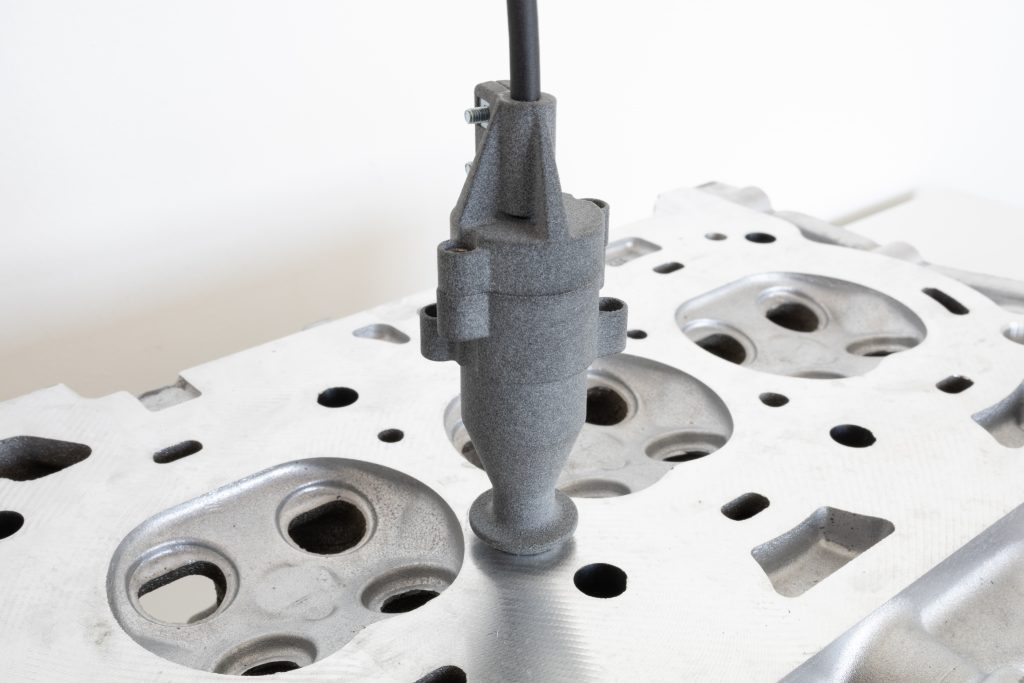
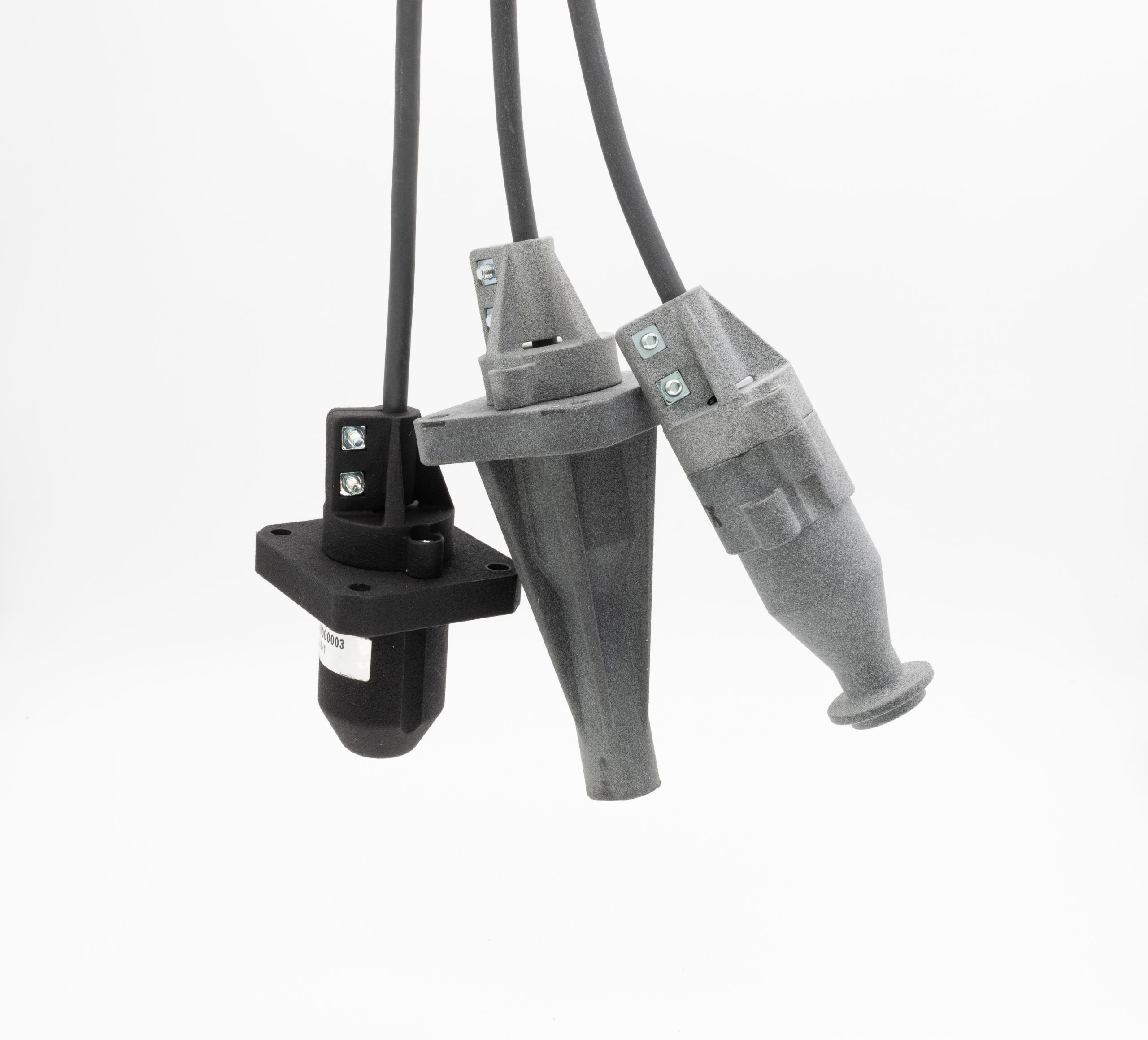
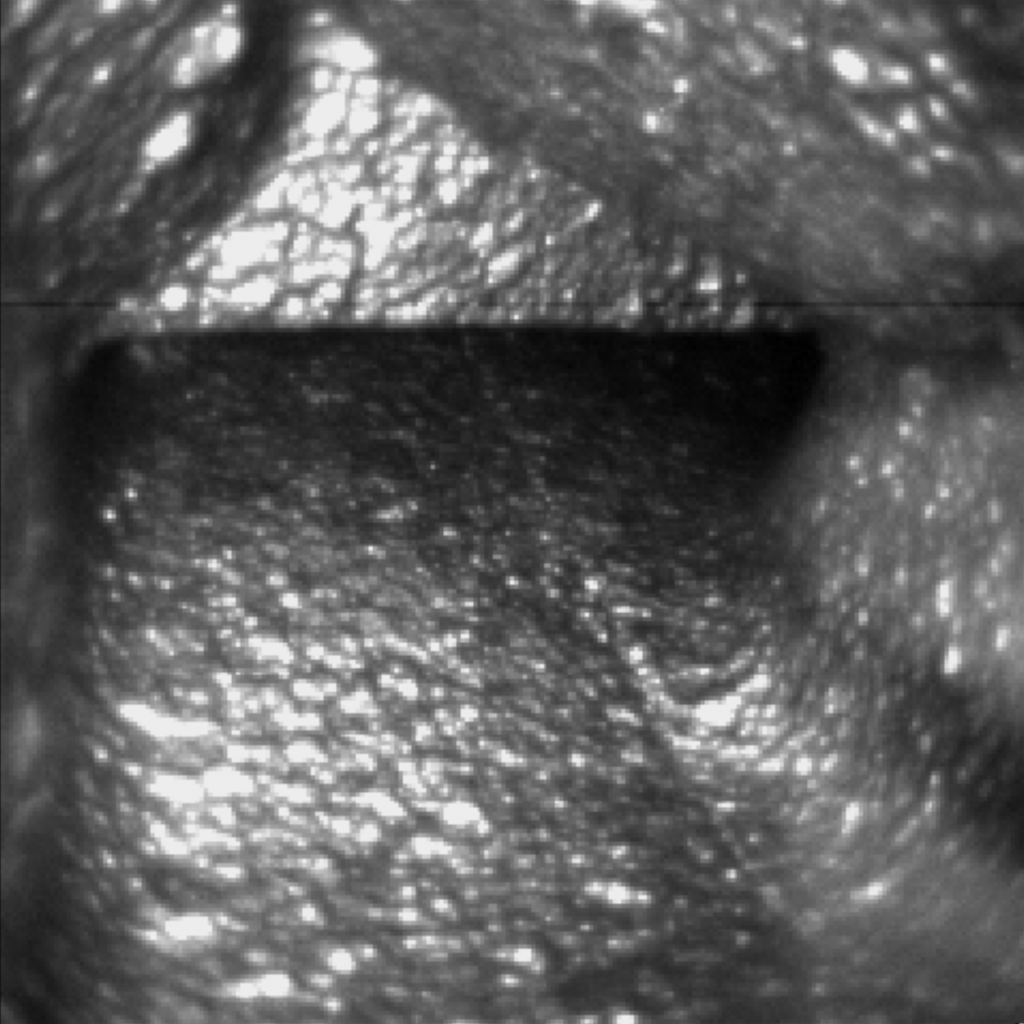
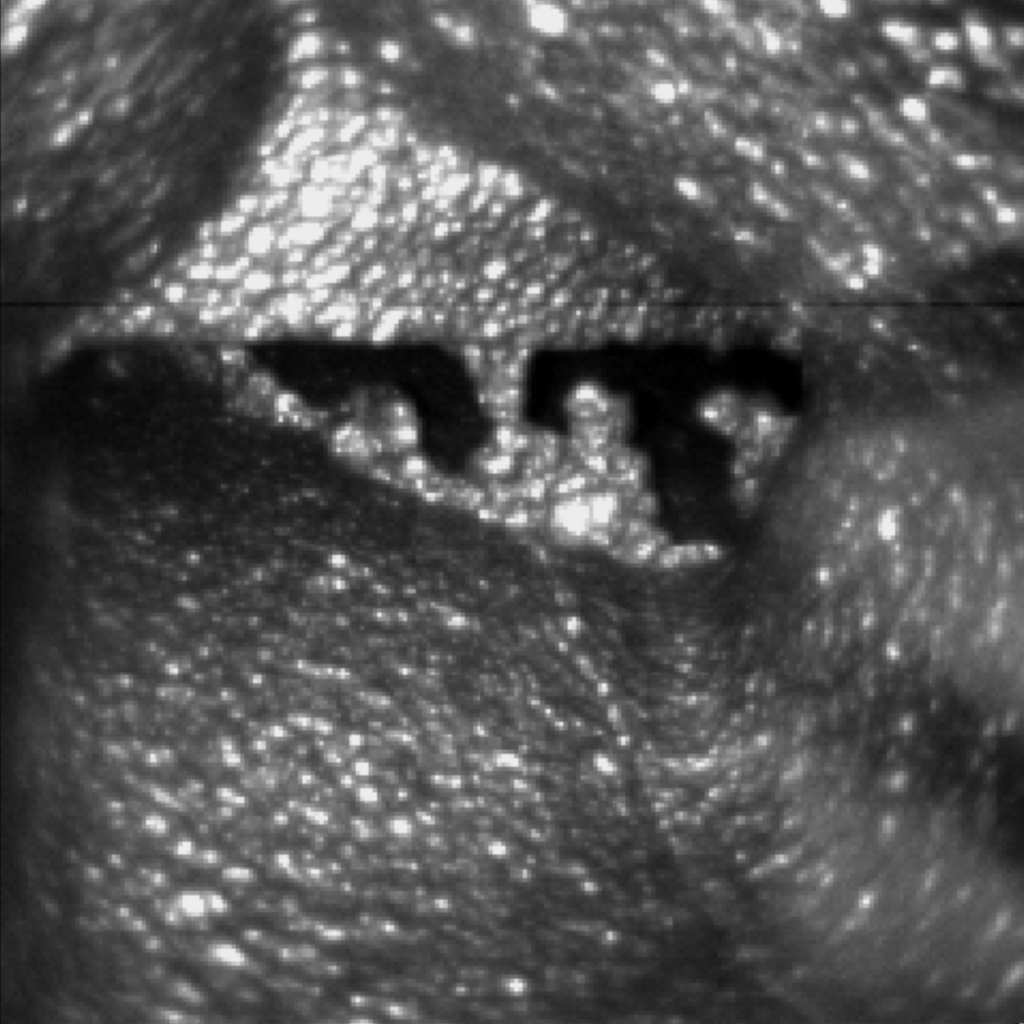
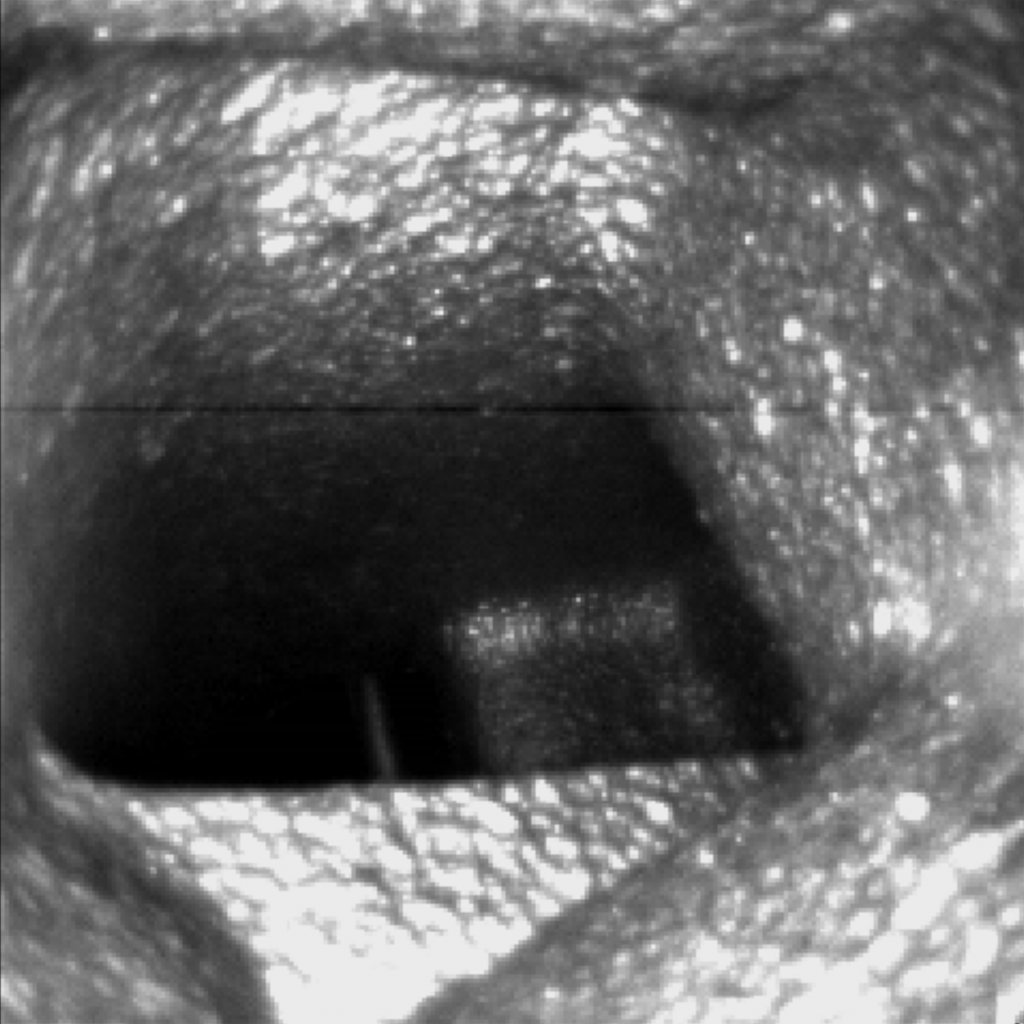

Detection Capabilities
- Full blockages
- Partial blockages (> 50%)
- Defects in split multi channels
- Undecored sand blobs
- Machining chips in narrow channels
- Wrong drill through connections
How does it work?
The Ionic system is based on ultrasonic technology. It operates on the principle of measuring a ultrasound passing through the channels of the casting. Our engineers design custom layout of probes for each project to maximize the coverage of inspected channels. Individual probes are mounted on a fixture that is aligned to the part openings to conduct the measurement. By measuring the signal intensity and time of signal propagation between selected transmitter-receiver pairs, the system evaluates the channel condition. Measurement is serialized with one transmitter working at a time, so defects can be clearly localized in the channel network. When the channels are completely blocked, the signal decreases to zero. Should the signal fall out of the standard process variation, the system will suspect partial blockage or other type of defect.
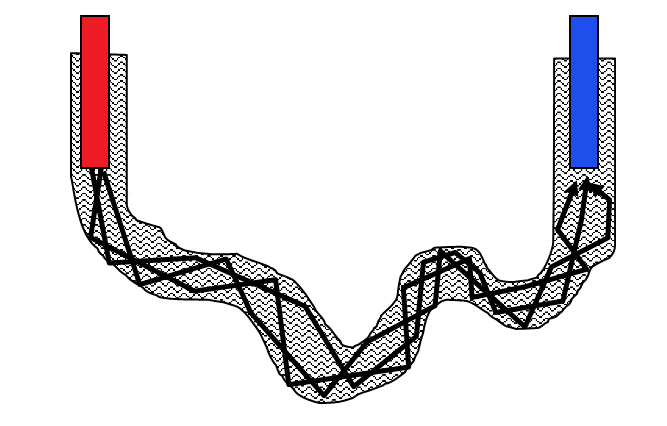
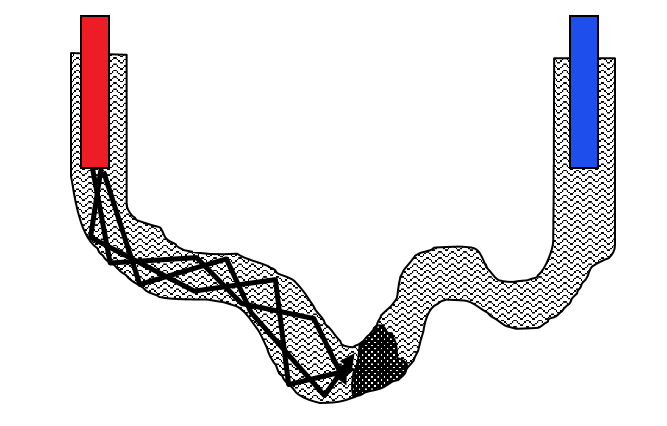
Benefits
- Inspection of complex channel geometries
- Increased maximum channel length
- Individual channel-by-channel measurement
- Result is not affected by the surface roughness & color
- Short cycle time (complete inspection within ~ 1-3 s)
- Universal probe design - less spare parts needed
- Increased lifetime of Probes – they do not enter inside the openings
System Parameters
Max. Ionic probes count:
unlimited
Signal source power:
PIN <= 0,5 W peak
Signal modulation:
variable frequency
Measurement cycle time:
10 ms per channel
Minimum opening size:
2 mm
Detection of full blockages:
100% zaručené
Detection of partial blockages:
>60% possible depending on the part design
Inspection capability:
on-demand. We will provide you the feasibility study for free.